Viet Nam is making efforts to adapt to new technologies in the fourth industrial revolution (Industry 4.0) across all sectors. President and CEO of General Electric (GE) Asia Pacific Wouter Van Wersch shared his views with Viet Nam News reporter Thu Giang about Viet Nam’s readiness to participate in the digital economy and GE’s action plan in the country.
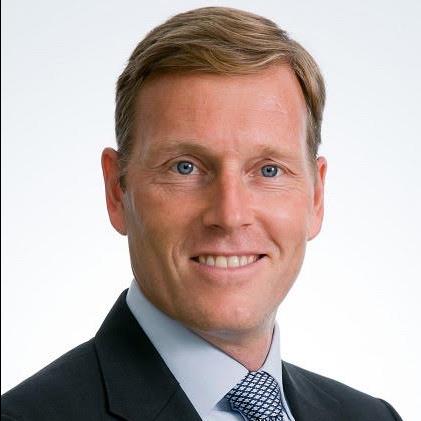
Viet Nam is making efforts to adapt to new technologies in the fourth industrial revolution (Industry 4.0) across all sectors. President and CEO of General Electric (GE) Asia Pacific Wouter Van Wersch shared his views with Viet Nam News reporter Thu Giang about Viet Nam’s readiness to participate in the digital economy and GE’s action plan in the country.
Can you evaluate Viet Nam’s adaptability to new technologies in the fourth industrial revolution?
GE sees that Viet Nam is embracing the trend with high commitment. A 2018 study by the Institute for Global Leadership under the US-based Tufts University showed Viet Nam ranks 48th out of 60 countries globally in terms of rapidly switching to a digital economy.
The Vietnamese market’s readiness is high with a large young population who can rapidly adapt to new technologies. The country has great potential to stand at the forefront of the trend with a high number of internet users and smartphone app usage, both in urban and rural areas. Viet Nam is also striving to become one of the world’s 10 largest nations producing software and providing digital content, with about one million people working in the IT sector by 2020.
That readiness and potential will build a solid springboard for the country to catch up with the revolution.
Speaking from a technological point of view, the digital revolution is changing the face of every industry. Besides bringing into Viet Nam relevant technology in power, renewables, healthcare and aviation, GE’s wind turbine generator manufacturing facility in Hai Phong is also at the forefront of this change. After 10 years of operation and two years of transformation, GE Haiphong is now a fully-fledged member of our five brilliant factories across the world, which make full use of connected digital solutions, advanced manufacturing and radical optimisation to stand on the front line of Industry 4.0. The plant has generated hundreds of millions of dollars in export revenue annually. It has also given Hai Phong and Viet Nam a much-needed and appreciated boost by bringing to the country world-class technology and management expertise while striving to ensure ample benefits trickle down to the local economy – not only in training and employment, but by the localisation of supply and the promotion of 4.0-compatible governance principles. This is a clear example of the adaptability of Viet Nam in the fourth industrial revolution.
Viet Nam’s Politburo has recently issued Resolution No 52-NQ/TW with a number of guidelines and policies to ensure active participation in Industry 4.0. In your opinion, what are the most important things to turn it into a reality?
Digitalisation is extremely powerful to help infrastructure stay agile and resilient for whatever that is coming. Modern society is incredibly complex. It will take years to discover how to fully exploit the new capabilities in products and services and to then develop organisations that can deliver them. Earlier industrial revolutions played out over decades. There is no reason to think that this one will be different. But one thing is certain, those who lead in embracing the new digital business playbook will see strong advances.
From our experience in digital transformation around the world, industry/innovation collaboration and developing workforces of the future are critical. The digital journey requires industry-wide collaboration; start-ups, governments and multi-national corporations are required co-create technologies together. All sectors –private, public and academia –have a shared responsibility to close the skills gap and make sure our workforce is prepared for the future. We’re doing our part by actively investing in developing the workforce of the future through training, attracting new talent and encouraging innovation across our global workforce.
What challenges does Viet Nam face in the digital transformation?
It is very encouraging that the Vietnamese Government includes digital transformation as a target in its development agenda. I think one of the key challenges with digital transformation is that there is no “one-size-fits-all” solution or a recipe for success. Digital transformation is a learning process for all parties involved, knowledge is the ultimate power, and the will and skill of people to embrace the change is critical. The ability to use and make the most of technology is also important, which could be fostered through education policies that focus on skills developments. Digital transformation is not happening overnight. It requires collaboration across all sectors and it usually takes time to prepare the workforce.
Finally, the digital transformation must be balanced with sustainable development and to be an instrument to ensure sustainability. Thus, more creativity and responsibility will be required to integrate sustainable benefits into new innovations.
Can you share with us GE’s action plan in the Vietnamese market?
GE helps generate more than 30 per cent of Viet Nam’s power capacity and our equipment is powering many key energy projects, from thermal to hydropower. Renewable energy is also something we are involved in and demand has great potential. We have also helped upgrade thousands of kilometres of national transmission lines and have supplied transmission equipment to many projects in Viet Nam.
In healthcare, more than 50 per cent of hospitals around the country use at least one piece of GE’s healthcare technology every single day. Our aircraft technologies, meanwhile, are also helping Vietnam Airlines, Vietjet and Bamboo Airways operate their aircraft engines.
Viet Nam will continue to experience an increase in the size of its middle class. This requires not only greater access to healthcare but also better healthcare. I think GE’s healthcare business will play a critical role in public-private partnerships with hospitals to guarantee that Vietnamese people obtain the level of healthcare they need.
Viet Nam will also continue to see rising demand for power, like the rest of the world, but must address its energy mix and challenges in terms of the environment and the need to reduce emissions as soon as possible. This means increasing the use of renewable energy, gas and other environmentally-friendly sources of energy. The use of more efficient technology such as the 9HA gas turbine is also critical in helping the government archiving its energy target.
Meanwhile, Viet Nam’s aviation industry is poised for strong growth, and the number of air passengers is expected to triple between now and 2030. As more people fly, airlines are likely to expand their fleets and that is good news for high-quality engine makers like GE. That’s a huge growth opportunity for us in Viet Nam, and also why we’re eager to partner with airlines here.
Are you going to open training courses for Vietnamese staff in the future?
Globally, GE invests US$1 billion each year on training and education, making us the world’s best company for leaders in 2015. GE offers numerous development, training and leadership programmes to our employees across the region, including Viet Nam.
As a company, GE believes in a tailored approach for every country, we call it a “Company to Country” approach. We adopt our approach and strategy in Viet Nam and in other countries, looking at what is needed to support development and making sure we bring the right solutions. In order to do that, it is critical to build a strong local team and I’m very proud that 100 per cent of our 2,000 employees in Viet Nam are Vietnamese.
The biggest advantage of having a strong local team is the local insight. Meanwhile, GE’s learning and development system equips leaders with the necessary knowledge and skills that enable them to grow and work more efficiently. GE also provides customised training programmes (both technical and soft skills) for individual development at various stages on the career ladder. — VNS